Traditional open differentials, while effective in allowing the left and right wheels to rotate at different speeds during cornering, suffer significant limitations under conditions of low traction or single-wheel slippage. In such scenarios, torque is disproportionately distributed to the wheel with the least resistance, leading to a loss of effective driving force. To overcome this limitation, the Limited Slip Differential (LSD) was developed. Among various LSD types, the clutch-type mechanical LSD stands out due to its rapid response, mechanical simplicity, and independence from electronic controls. It is widely applied in motorsports, performance vehicles, and off-road platforms. This article presents a systematic analysis of its structural components, operating principles, and torque transfer mechanisms under dynamic conditions.
Structural Composition
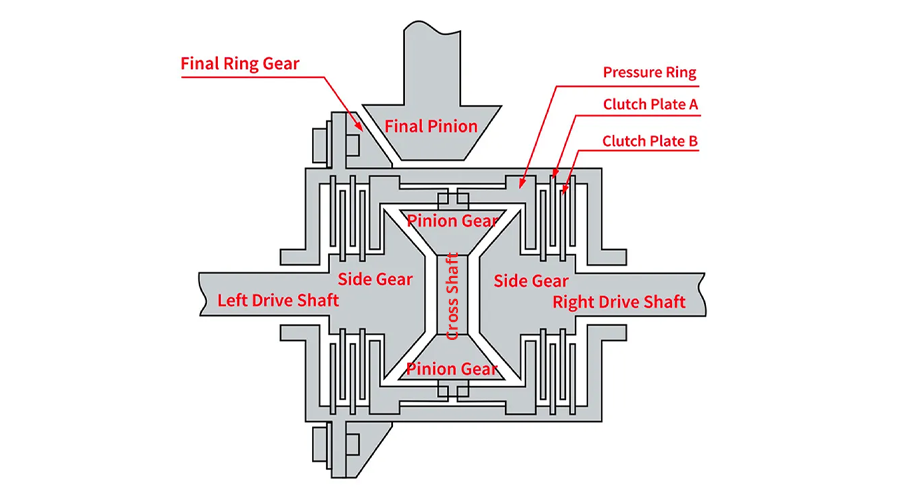
The differential case serves as the external housing, rigidly connected to the drivetrain (e.g., driveshaft or transmission output shaft), and transmits torque to the internal components. It features internal grooves and stop surfaces for the installation and axial guidance of the pressure plates and clutch pack.
The pressure plate is a metallic disc with specially machined grooves or ramps at its center, designed to interact with matching protrusions on the cross shaft. During operation, the relative rotation between the cross shaft and the pressure plate ramps converts rotational motion into axial displacement, enabling the pressure plate to compress the clutch pack.
Operating Principle and Dynamic Behavior
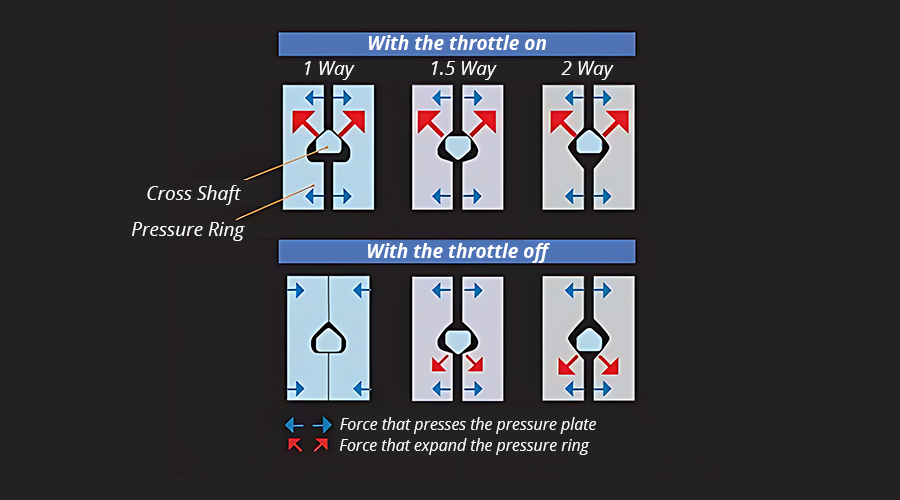
Performance Characteristics and Applications
In motorsports, two-way LSDs provide consistent lock-up during both acceleration and deceleration, enhancing cornering stability and rear-end control. In road and mountain driving scenarios, 1.5-way LSDs offer a balance of stability and drivability by reducing locking strength during braking. While Torsen (torque-sensing) differentials are often favored in all-wheel drive and variable road conditions due to their self-adaptive characteristics, clutch-type LSDs remain valuable where deterministic and tunable locking behavior is required, particularly in racing or off-road competition.